Simply work cleanly
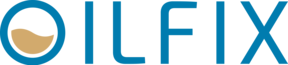
Hydraulic hoses on construction machinery can be damaged by the effects of weather, material fatigue or external influences in everyday construction site use. The exposed high-volume flow lines of the auxiliary hydraulics are particularly susceptible to such damage. Defective or torn hose lines lead to uncontrolled leakage of hydraulic oil during excavator operation.
Previously, such leaks could only be stopped manually after the boom had been lowered and the excavator switched off. Valuable time is lost during which further oil escapes.
With Oilfix, the auxiliary hydraulics line can be shut off directly from the driver's cab at the touch of a button to stop the uncontrolled oil leakage immediately.
Oil stop at the touch of a button
OILFIX valve blocks are mounted in pairs on the excavator boom and replace the standard ball valves.
By installing Oilfix in the past, future damage is significantly reduced - as often as required.
Once the defective hydraulic line has been repaired, the complete oil circuit can be re-opened at the touch of a button. OILFIX is then immediately ready for use again to prevent major damage the next time a hose bursts.
Simply explained
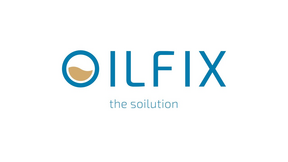
We use a third-party service to embed video content. This service may collect data about your activities. Please read the details and agree to use the service to view this video.
Your questions
Our answers
Hydraulic systems turn various machines into real commercial vehicles, be it construction, agricultural or forestry machinery, lorries or trailers. The hydraulic oil required for power transmission is pumped through special lines in the form of pipes or hoses. Hydraulic hoses in moving parts of machines age naturally due to sunlight, dirt or material fatigue. The DGUV recommends maintenance intervals to prevent hose bursts during normal operation. However, most hose bursts in practice are caused by external influences; for example, when a demolition excavator gets caught on a piece of steel and individual hoses are torn off. Uncontrolled oil leaks from defective or torn pipes can lead to environmental damage, consequential costs and increased health risks. OILFIX can significantly reduce oil leakage in the event of a hose burst. The operator can move the excavator to a suitable location without further oil leaking, limiting contamination and speeding up clean-up operations. This minimises downtime and significantly reduces the negative impact on project progress and the construction site result.
OILFIX valve blocks are mounted on both sides of the excavator boom and replace the conventional mechanical shut-off valves. They are connected to the driver's cab via an electrical cable. In the event of a leak, machine operators can intervene immediately at the touch of a button and stop the oil leakage instantly to minimise the extent of the damage. Despite the lines being shut off, the excavator remains functional so that the machine can continue to be operated and moved to a repairable state without any further oil leaks. When the excavator is in a suitable repair or parking position, defective hose material can be replaced as usual so that the excavator can be fully utilised again. Once the hydraulic hose has been repaired or replaced, the hydraulic oil circuit can be reopened at the touch of a button. OILFIX is then immediately ready for use again to prevent major damage the next time the hose bursts.
Pipe rupture safety valves have proven themselves as indispensable safety valves for holding the load. In the event of a pipe bursting on the excavator, these components prevent the boom from dropping in an uncontrolled manner and thus significantly reduce the risk of injury to site personnel. However, uncontrolled oil leakage is not stopped in the event of a pipe burst, despite the excavator arm being locked in position, meaning that further (environmental) damage is caused every second. This is exactly where OILFIX comes in: The switch in the driver's cab can stop the oil leakage immediately.
Despite preventive measures and careful working methods, hose bursts are part of everyday life on construction sites. To significantly minimise the consequences of a hose burst, OILFIX can be used several times after installation: By confirming the switch in the driver's cab, the working voltage prevailing during normal operation is immediately switched off and the OILFIX valve is closed on both sides. Once the defective hose has been repaired or replaced, the affected lines can be re-opened by pressing the OILFIX switch again. The complete hydraulic oil circuit is restored. Thanks to the one-off installation of OILFIX, excavators and operating personnel are prepared for the next hose burst.
Born on the building site.
The idea for OILFIX?
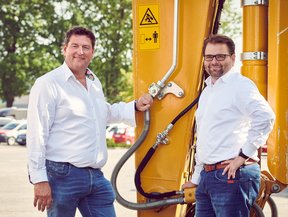
OILFIX inventor Berthold Winz has been working with construction and agricultural machinery for more than three decades and specialises in sensitive demolition and special inner-city demolition work. As a passionate machinist and successful entrepreneur, he has experienced leaks with costly consequences many times. For the problem solver, the consequences caused by hose bursts were no longer acceptable. The trained agricultural machinery mechanic set to work and developed the idea for OILFIX.
For the successful further development and marketing of the product, Berthold Winz combined his practical construction site experience with Christoph Sauer's commercial flair. The tech-savvy logistics expert was quickly impressed by the innovative idea and took over the realisation until it was ready for the market. Together, the managing director tandem founded OILFIX GmbH in 2023 to make construction work more ecological and economical at the same time. With a well-organised team, OILFIX solves the well-known problem of hose bursts ‘at the touch of a button’.
Do you have a question?
Feel free to contact us
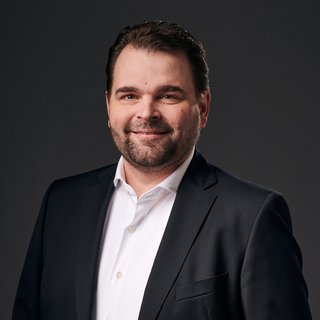
Christoph Sauer
Geschäftsführer OILFIX GmbH
Schleyerhofweg 6 50829 Köln